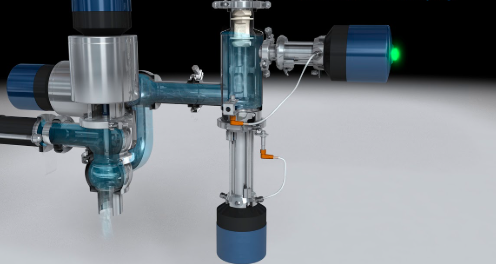
Maximizing Profit with Product Recovery System ROI
In industries where products are manufactured or processed, maintaining a consistent and efficient operation is key to profitability. A product recovery system is a technology designed to recover and reuse materials or products that would otherwise be discarded during the manufacturing or processing stages. These systems have gained significant attention due to their ability to enhance operational efficiency, reduce waste, and significantly improve the return on investment (ROI) for businesses. This article explores how implementing a product recovery system can lead to increased profitability, sustainability, and long-term business success.
Understanding Product Recovery Systems
A product recovery system is a solution used to capture and retrieve products, raw materials, or by-products that would normally be lost during the production process. These systems can be employed across various industries, including food and beverage, pharmaceuticals, chemical processing, and manufacturing, to reduce waste and improve the efficiency of operations.
These systems often involve the use of specialized product recovery system roi equipment, such as filters, separators, pumps, or conveyors, to recover valuable materials. By implementing such systems, companies can minimize losses and maximize the utilization of their resources, ultimately increasing their ROI.
How Product Recovery Systems Improve ROI
While investing in a product recovery system may involve upfront capital costs, the long-term benefits are substantial. These systems enhance productivity, reduce waste, and lower operational costs, all of which contribute to a more favorable ROI. Below are the key ways in which a product recovery system can enhance ROI:
1. Minimizing Product Waste
In many production processes, a certain amount of product or material is inevitably lost due to inefficiencies, spillage, or waste. This loss can result in increased material costs and lower profitability. A product recovery system helps reduce this waste by capturing and reusing materials that would otherwise be discarded.
For example, in the food and beverage industry, a significant portion of the raw ingredients or finished product may be lost during processing. With a product recovery system in place, businesses can reclaim a substantial portion of this lost product, reducing material costs and increasing profitability.
Similarly, in the chemical and pharmaceutical industries, product losses can be costly and may even compromise production quotas. A product recovery system ensures that valuable raw materials and by-products are not wasted, contributing to cost savings and better utilization of resources.
2. Reducing Operational Costs
The cost of materials and products can account for a large portion of a company’s operational expenses. By recovering and reusing valuable resources, a product recovery system helps businesses reduce the amount of raw materials they need to purchase, thus lowering costs.
In addition to material savings, product recovery systems often streamline production processes, making operations more efficient. For instance, by automating the recovery process, companies can reduce the need for manual labor and minimize downtime associated with handling product waste. This leads to overall operational cost reductions, which further improves ROI.
3. Improving Product Quality and Consistency
A product recovery system also plays a crucial role in ensuring the quality and consistency of products. During production, some materials or products may become contaminated or degraded, leading to inconsistent output. By recovering usable materials and reintroducing them into the production process, businesses can ensure that the final product meets high-quality standards.
For example, in the pharmaceutical industry, maintaining consistency is essential for meeting regulatory standards and delivering safe products to consumers. By using a product recovery system, pharmaceutical companies can reclaim materials that meet the required specifications, ensuring uniformity and quality in their output. This minimizes the risk of product failures, recalls, or compliance issues, all of which can be costly.
4. Boosting Sustainability Efforts
In today’s environmentally conscious market, businesses are increasingly looking for ways to reduce their environmental footprint. Product recovery systems contribute to sustainability by minimizing waste, reducing the need for new raw materials, and lowering energy consumption.
By recovering and reusing materials, companies can minimize their reliance on external suppliers for raw materials, contributing to a reduction in transportation emissions and resource extraction. This not only benefits the environment but can also enhance a company’s reputation as a responsible and eco-friendly business, appealing to customers who prioritize sustainability.
Moreover, reducing waste through product recovery systems can help businesses comply with environmental regulations and avoid penalties for excessive waste disposal. These sustainability efforts can result in long-term savings, further improving ROI.
5. Enhancing Production Efficiency
Product recovery systems help optimize production efficiency by ensuring that valuable resources are efficiently utilized. Instead of wasting time and resources on disposing of unused or excess product, businesses can focus on maximizing the productivity of their operations.
Read also: Things To Consider When Choosing Data Room Services For Your Business
For instance, in industries where production cycles are time-sensitive, such as pharmaceuticals and food processing, the use of a product recovery system can significantly reduce bottlenecks in the production line. The system ensures that any recovered product is quickly processed and reintroduced into the production flow, minimizing delays and increasing throughput.
This improved efficiency translates into higher production output and reduced lead times, both of which directly contribute to increased profitability and a more favorable ROI.
Conclusion
Investing in a product recovery system offers businesses the opportunity to significantly enhance their return on investment. By minimizing waste, reducing operational costs, improving product quality, and boosting sustainability efforts, these systems provide a comprehensive solution to optimize production processes. Moreover, the ability to recover valuable resources and reintroduce them into the production cycle ensures that businesses can maintain cost-effective operations while enhancing profitability.
From improving production efficiency to ensuring regulatory compliance and extending equipment life, the benefits of implementing a product recovery system are undeniable. Companies that incorporate these systems into their operations are well-positioned to achieve long-term profitability and sustainability, making the ROI from product recovery systems a valuable investment for businesses across various industries.